Porosity in Welding: Identifying Common Issues and Implementing Best Practices for Avoidance
Porosity in welding is a prevalent issue that usually goes unnoticed till it triggers substantial troubles with the stability of welds. This typical problem can endanger the strength and resilience of welded structures, posturing safety and security threats and leading to pricey rework. By comprehending the root triggers of porosity and implementing reliable prevention approaches, welders can considerably improve the top quality and dependability of their welds. In this discussion, we will discover the crucial factors adding to porosity formation, analyze its harmful results on weld performance, and review the ideal methods that can be adopted to minimize porosity event in welding procedures.
Typical Root Causes Of Porosity

Another frequent perpetrator behind porosity is the presence of contaminants on the surface of the base metal, such as oil, grease, or corrosion. When these impurities are not efficiently eliminated prior to welding, they can evaporate and become trapped in the weld, causing problems. Using filthy or wet filler materials can present contaminations right into the weld, adding to porosity issues. To reduce these typical reasons of porosity, detailed cleansing of base steels, proper securing gas selection, and adherence to optimum welding parameters are necessary methods in achieving high-grade, porosity-free welds.
Effect of Porosity on Weld Top Quality

The existence of porosity in welding can considerably endanger the structural honesty and mechanical residential or commercial properties of bonded joints. Porosity creates gaps within the weld steel, deteriorating its general toughness and load-bearing capacity.
Welds with high porosity levels often tend to show lower influence strength and reduced capacity to flaw plastically before fracturing. Porosity can impede the weld's capability to properly transfer pressures, leading to premature weld failure and prospective safety and security hazards in critical frameworks.
Best Practices for Porosity Prevention
To enhance the structural integrity and top quality of bonded joints, what specific actions can be carried out to minimize the incident of my explanation porosity during the welding process? Making use of the right welding technique for the particular product being welded, such as readjusting the welding angle and weapon setting, can further protect against porosity. Normal inspection of welds and prompt removal of any kind of issues identified throughout the welding process are important methods to prevent porosity and generate premium welds.
Relevance of Proper Welding Strategies
Applying proper welding methods is vital in making sure the architectural integrity and quality of bonded joints, building upon the structure of efficient porosity prevention steps. Excessive heat can lead to raised porosity due to the entrapment of gases in the weld swimming pool. Furthermore, utilizing the appropriate welding parameters, such as voltage, current, and travel rate, is crucial for accomplishing sound welds with minimal porosity.
Furthermore, the option of welding procedure, whether it be MIG, TIG, or stick welding, must straighten with the details needs of the task to make sure optimum outcomes. Appropriate cleansing and preparation of the base steel, along with choosing the right filler product, are additionally essential parts of skillful welding techniques. By sticking to these finest methods, welders can decrease the danger of porosity development and create high-grade, structurally audio welds.
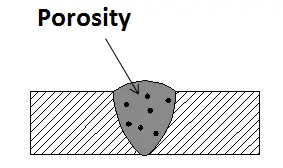
Checking and Quality Control Measures
Checking procedures are necessary to discover and avoid porosity in welding, ensuring the strength and toughness of the last product. Non-destructive screening techniques such as ultrasonic testing, radiographic screening, and visual examination are commonly employed to identify possible flaws like porosity.
Performing pre-weld and post-weld inspections is also critical in keeping quality assurance standards. Pre-weld evaluations involve validating the products, tools settings, and sanitation of the workspace to stop contamination. Post-weld evaluations, on the other hand, evaluate the final weld for any kind of issues, including porosity, and validate that it meets defined criteria. Executing a comprehensive quality assurance strategy that includes complete screening procedures and assessments is paramount to i thought about this decreasing porosity issues and ensuring the overall high quality of bonded joints.
Final Thought
To conclude, porosity in welding can be an usual problem that influences the quality of welds. By identifying the common reasons of porosity and applying best practices for prevention, such as correct welding strategies and testing measures, welders can make sure top quality and reputable welds. It is vital to focus on avoidance methods to lessen that site the occurrence of porosity and maintain the stability of welded structures.